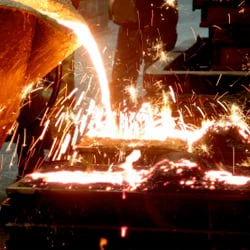
Building the Next Generation of PLC Cable for a Large Integrated Steel Mill
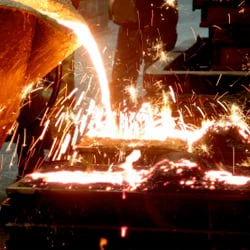
With no drawings to work from, RESCO reverse-engineered an old PLC cable to develop a new prototype that was more cost-effective and reliable. But RESCO’s customer also got something more in the bargain— a set of reliable specifications they could use going forward.
Our customer, one of the world’s largest integrated steel producers, needed a uniquely configured cable assembly that connects a master Programmable Logic Controller to a large mill ladle that holds tons of molten steel. The PLC controls the movement of the ladle from the furnace to the pour station. Since the cable is used in the harsh environment of the mill, cables wear out quickly and must be replaced frequently. The customer was building the cables in-house at considerable expense. Complicating the task was the complexity of the cable assembly and the lack of any written specifications.
Our customer knew that we were capable of building this type of assembly but did not realize the time and expense that could be saved by using RESCO. Since no formal specification or drawings had ever been produced, we had to reverse-engineer an old cable. Though the reverse engineering process was difficult and tedious, it gave us the unforeseen opportunity to improve the design and create the written specifications so critically needed.
Using wiring diagrams, old parts orders, and in-depth interviews with the maintenance and engineering staff, we built a new, improved prototype. The new cables have a longer life, less downtime, and are delivered at a lower total cost than the originals. Making the program even more appealing to our customer, RESCO stocks the component parts for rapid builds of replacement cables so the mill is no longer burdened with the cost of maintaining an inventory of replacement parts and cables.
You May Like
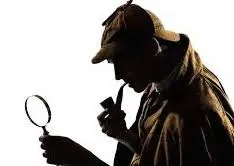
The Case of the Rusty Temperature Sensor
The Problem Several years back, I was contacted by one of our customers that needed a temperature sensor for a deionized (DI) water tank. Although we have helped this customer engineer several different sensors over the years, RESCO had not been involved in this design. Our customer is a Fortune
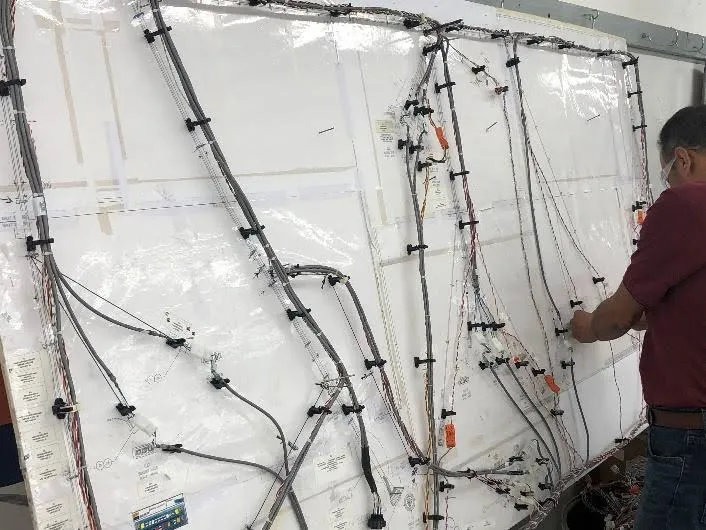
Engaging During the Design Process Pays Big Dividends
RESCO Electronics and a leading manufacturer of diagnostic and treatment equipment for women have a relationship dating back 25 years. For any relationship to last that long, it requires a great deal of work and trust on both sides. Recently when this customer was developing a new platform, RESCO collaborated
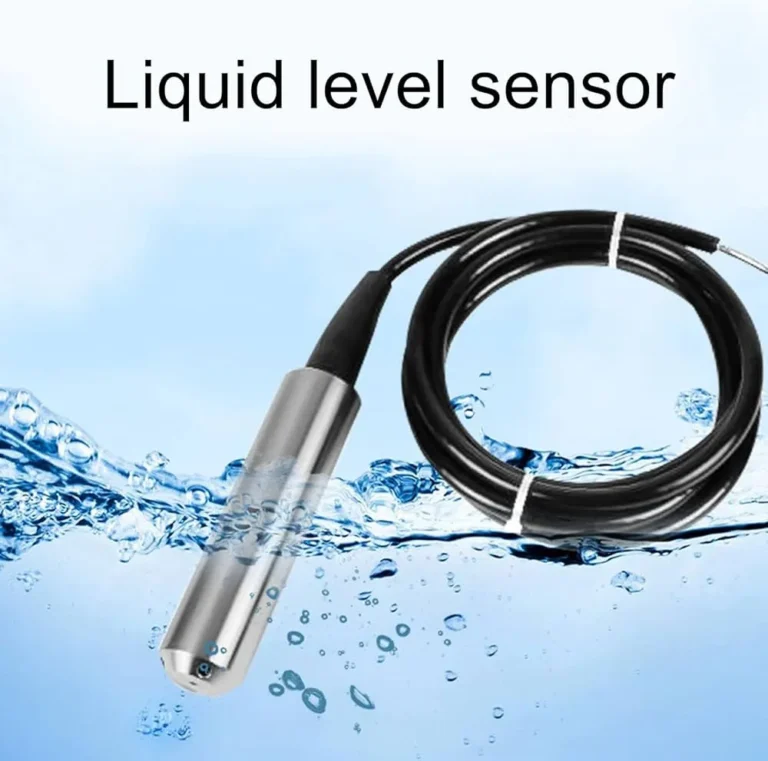
Providing Field Service a Tool to Be More Productive
Starting with only a few rough sketches, RESCO provided a liquid level indicator that produced an almost immediate return on this customer’s investment. A major clinical diagnostic company wanted its field service technicians to be able to measure a critical liquid level in an instrument quickly and accurately. Unfortunately, the