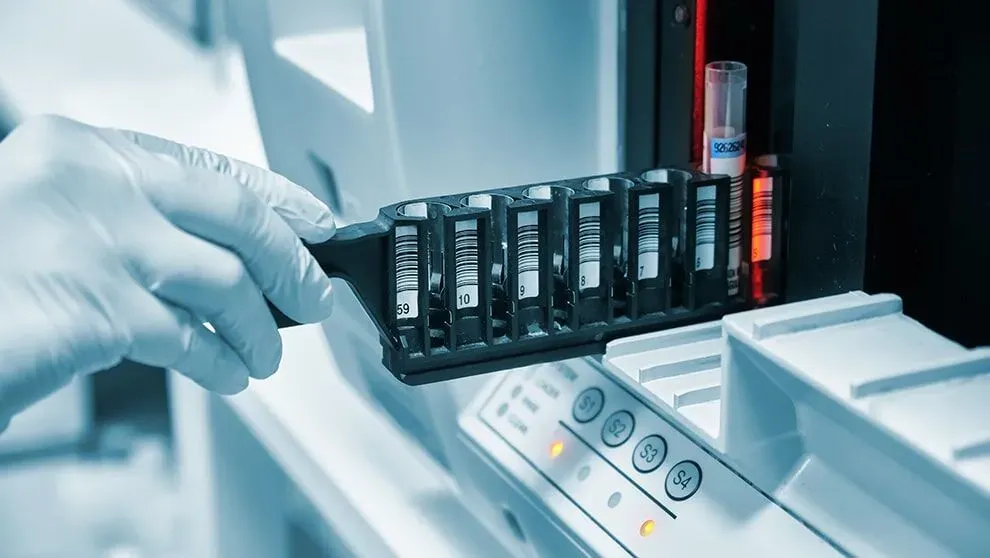
Fixed Position Scanner Obsolete…No Problem!
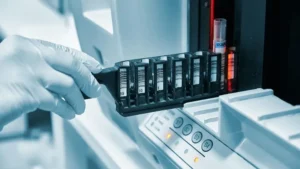
For several years RESCO has supplied a barcode reader to a medical equipment manufacturer for an instrument that they produced in the United States. When this same customer had an obsolescence issue on a different micro-biology platform, they reached out to the RESCO team for a solution.
This obsolete scanner was a fixed position, embedded application and, as a result, there were several difficult challenges in finding a replacement. First, the new scanner had to fit in the same space allocated for the old scanner. Second, the new scanner had to be approximately the same focal distance from the target barcode as the scanner it would replace. Last, and most challenging, the new scanner had to function without a change to the instrument’s software. All of these challenges needed to be overcome in time to fully test and validate the new scanner before the supply of the old scanner ran out.
Working closely with the sustaining engineering team at our customer, RESCO and our partner Opticon were able to provide a solution that included:
- A custom designed interface board that would mount into existing space. This interface board was able to replicate the signals and power requirements of the existing product. The board also included the custom firmware that eliminated the need for the customer to change their instrument software. Because of this, the RESCO solution not only supports new production, it also seamlessly supports service spares.
- The required mechanical information to allow our customer’s engineers to design a bracket that supported new production as well as service spares.
- First article units for burn in testing.
- Detailed specifications, including all firmware and settings data so the exact manufacturing specifications could be locked in and subject to strict revision control.
Because fixed position scanner solutions are a combination of mechanical, electrical and software engineering, there are usually tweaks and minor modifications required after the initial engineering prototype. Working both onsite with our customer and remotely from RESCO, we were able to quickly support these minor modifications allowing our customer to implement the needed changes in production and field service with no disruption.
During a time of rising costs, our customer expected the new scanner to be more expensive than the one it replaced. In fact, the opposite was true. This solution netted our customer a 13% cost reduction adding icing on the cake of a very successful project.
You May Like
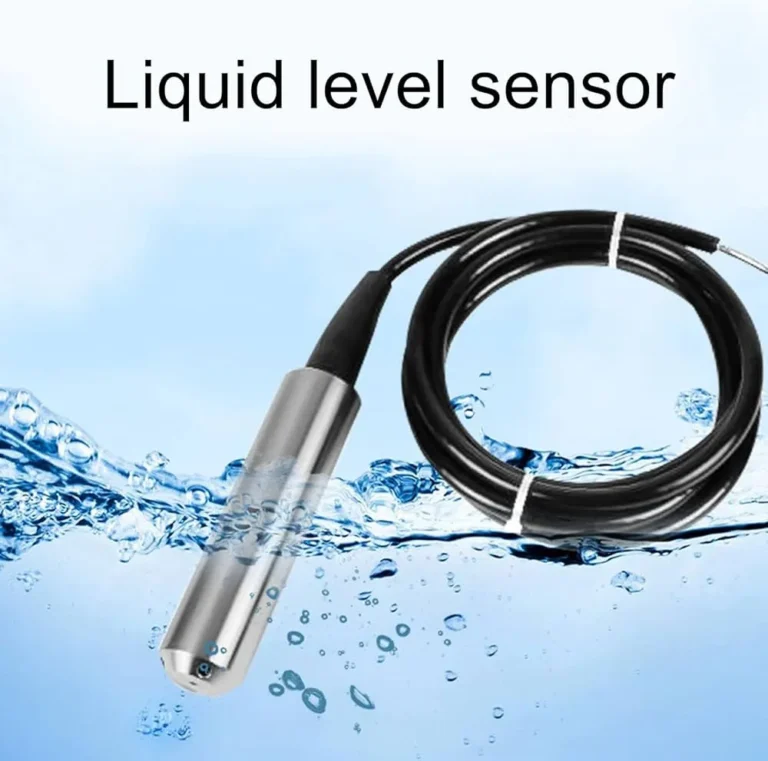
Providing Field Service a Tool to Be More Productive
Starting with only a few rough sketches, RESCO provided a liquid level indicator that produced an almost immediate return on this customer’s investment. A major clinical diagnostic company wanted its field service technicians to be able to measure a critical liquid level in an instrument quickly and accurately. Unfortunately, the
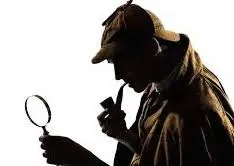
The Case of the Rusty Temperature Sensor
The Problem Several years back, I was contacted by one of our customers that needed a temperature sensor for a deionized (DI) water tank. Although we have helped this customer engineer several different sensors over the years, RESCO had not been involved in this design. Our customer is a Fortune
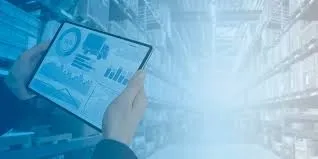
Taking Inventory (and Getting It under Control)
When increasing supplier lead-times and a need to reduce investment in inventory occurred at the same time, this defense contractor had a real challenge; a challenge that RESCO helped them overcome. A defense contractor that develops microwave sub-systems for military equipment was experiencing long lead-times and production shutdowns due to